A relationship between precision and heritage can be heard with each strike of a TAMA drum. Let’s uncover the history of this premium percussion brand.
As the executive manager of TAMA, Takanori Hoshino explains, ‘ichi-go ichi-e’ is a Japanese term that’s defined as “a once-in-a-lifetime encounter that is never repeated”. This is something the world-class music manufacturer aspires to achieve with each drum they construct, a unique musical journey capable of being sculpted to the player. Combining innovation with a deep heritage and culture is what TAMA is all about, and it’s part of what has kept them at the top of the percussive world since their humble beginnings.
Despite being much younger than some of their main competitors, the Japanese company has had its logo plastered on the badges, front heads and musical minds of some of the most famous drummers the world has ever seen, as well as millions of others, from beginner to expert. This is the story of TAMA drums, exploring how and why they’ve become the percussion giant they are today.
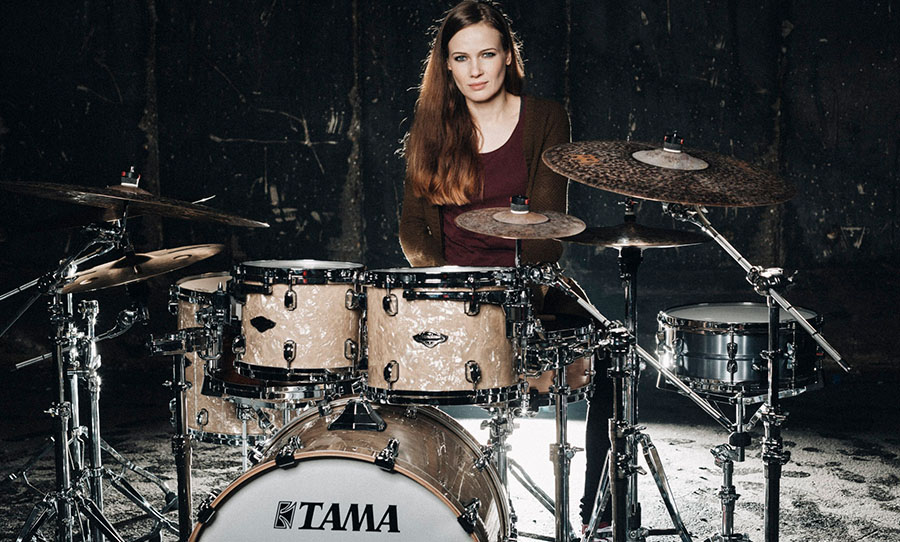
Photo: Mario Schmitt
An ever-expanding heritage
TAMA started out under a different title altogether, Star drums, named after the term ‘star field’, the English translation of founding company Hoshino Gakki’s family name. These drums were constructed at Hoshino’s subsidiary, TAMA Seisakusho, a factory that opened in 1962 with the main intent of manufacturing Ibanez guitars and amps.
However, by 1966, the construction of Ibanez products had moved elsewhere, and the construction of Star drums had grown. The premium offerings — the Imperial Star and Royal Star — were then offered in the US and saw success by providing a cheaper, yet high-quality alternative to the established drum companies of the time: Ludwig, Rogers and Slingerland.
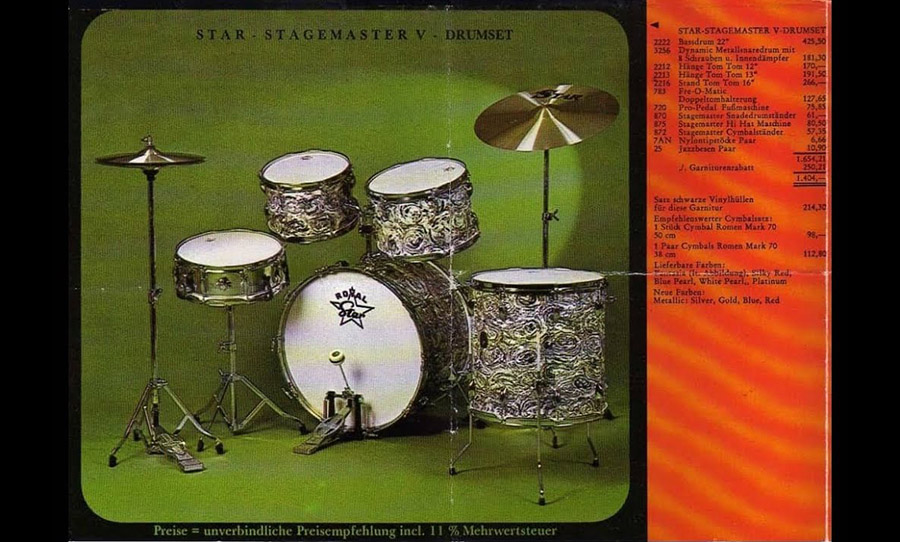
As this success continued, Hoshino changed the name of the company to TAMA in 1974, after the owner’s wife. Tama means jewel in Japanese, which was intended to reflect the premium quality and image of the company.
TAMA was quickly becoming a force to be reckoned with, a force that was only to be made stronger with their joint acquisition of Camco with Drum Workshop (DW) in 1977. DW acquired the tooling and manufacturing means while TAMA acquired the Camco brand and name, designs and patents. Camco’s remains had a lot to offer, and were known for having the best drum pedal on the market.
Both companies rereleased this pedal — DW with the DW5000, while TAMA kept the Camco name (it became colloquially known as the ‘Tamco’ pedal). TAMA drums skyrocketed in quality rapidly, and caught the eye of famous drummers around the world, boasting a combination of world-class construction and hardware, with a much more affordable price tag.
Drummers such as Stewart Copeland of The Police switched from his reliable Ludwigs to these new TAMAs that everyone was talking about. In an interview with Sweetwater, he says, “One day, I get these Japanese drums. And this was a time when Japan wasn’t known for high-precision industrial product. Suddenly, in that environment, these TAMA drums arrived, which were absolutely superior! These Japanese drums were better made, better designed, and had more substantial stands. It was like, “this is a drum set that landed from Mars! This is totally next level.” The sound of the tom-toms was an explosion, but with a definition of sound.”
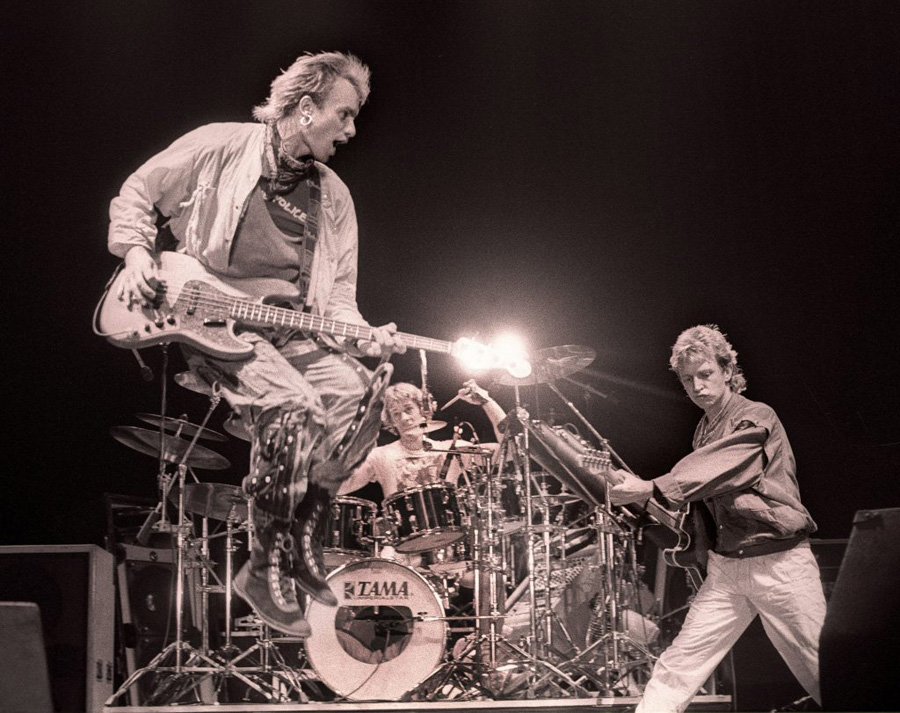
Innovation was at the heart of the TAMA image, even this early in its history. By the late 1970s, TAMA had sought to rid the world of often unreliable and frail hardware, by offering ‘super heavy-duty’ stands with the ability to sit cymbals and drums and the exact position drummers needed, removing the need for compromise and making playing easier.
With no sign of slowing down, they quickly created a new style of drum that would help to define the sound of the late ’70s and ’80s; ‘the octoban’. The octoban is a drum that makes use of only a top head, not dissimilar to the already popular concert tom. But rather than varying pitch with diameter, all octobans were all 6 inches in diameter and were offered in varying lengths. The massive drum kits of the ’80s were often seen making use of octobans for the addition of high pitched, spacey sounds that we’re able to cut through the rest of the ensemble.
Baked to perfection
To ensure consistent quality and unrivalled resonance, TAMA drums are constructed carefully by hand, using tried and tested methods. Each ply is hand-cut to the exact dimensions of the drum, before being glued via a TAMA signature diagonal cut. Once assembled, a large cylinder is used to expand the centre of the drum, before being cooked in the oven for around 20 minutes, the first step in achieving that golden brown sound.
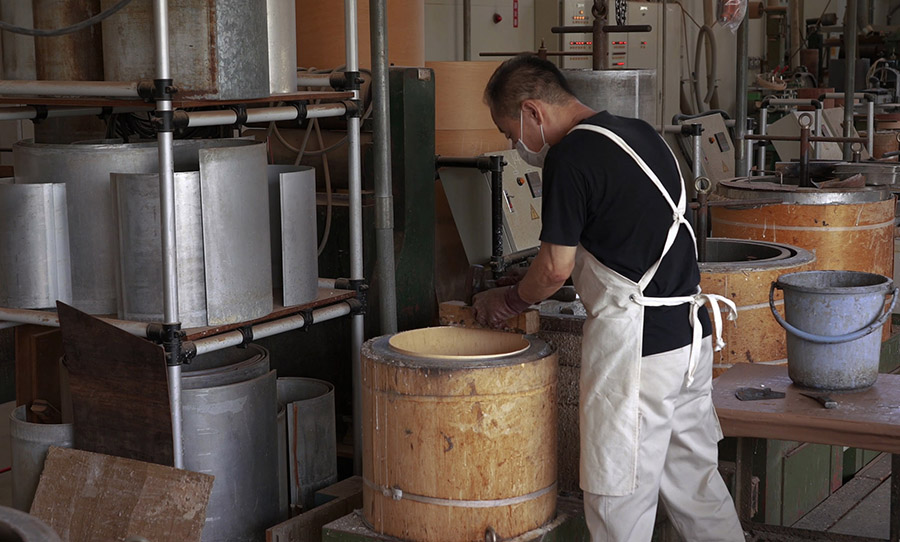
Photo: Drumeo
The drums are then sanded both inside and out, by machine and then by hand to ensure perfection. Once the makers are happy with their drum, they move on to the next stage. Maple and Bubinga drums feature sound focus rings, for added definition and durability. The rings are adjusted to ensure that they aren’t too loose or too tight. If the customer wishes, additional wooden inlays can be added.
The next stage is the addition of the signature TAMA decal and painting. Paint can indeed change the sound of the drum. An uneven application or the use of too much paint can severely affect the resonance of the drum. Once painted, the drums are then dried and cured, before being sanded.
The edge that the drum head sits against is called the bearing edge and is one of the most important stages in construction. The greater the distance between the outside of the shell and the point of contact with the head, the longer the drum will ring. Imperfections and anomalies in the bearing edge can be detrimental to the drum’s tuning ability and overall sound, so after they are machine cut, they are then adjusted and sanded by hand.
Finally, holes are drilled and the drum’s final assembly is completed. As they always have, TAMA makes use of the highest quality hardware, ensuring that the throw off is smooth and that hoops fit perfectly and allow for easy tuning.
The TAMA family roster
Some of the biggest drumming names have recognised TAMA’s supreme quality and distinct sound. Dave Grohl was known for using big TAMA drums during his time with Nirvana, an important addition to their heavy sound, with beefy toms and a birch snare with enough crack to make an omelette.
Similarly, the signature drum sound of Lars Ulrich and Metallica would not exist without the quality construction of TAMA drums. That being said, I wouldn’t blame the garbage bin lid like snare sound found on ‘St Anger‘ on TAMA, that one is all Lars.
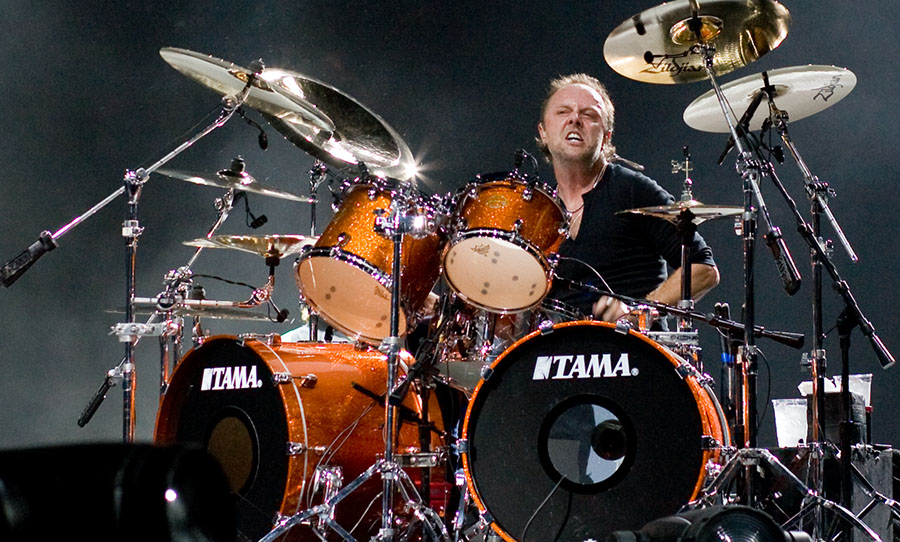
Photo: Kreepin Deth
With a range that accommodates drummers of all levels, TAMA truly is the percussion company for everyone. From the entry-level Rhythm Mate and StageStar ranges, to the boutique and luxurious Starclassics, regardless of the playing ability, budget or sound, TAMA has an answer that is sure to please everyone’s ears.
So if you’re after amazing quality drums, built with the finest care and the guarantee to meet your needs, it’s unlikely that you need to look anywhere past the TAMA range. To learn more, head over to the TAMA website.