Neumann has been at the pinnacle of microphone technology for decades. We chat with new CEO Ralf Oehl about the company’s unparalleled legacy and plans for the future.
Since the dawn of the recording industry as we know it, Neumann has been restlessly innovating in order to create the finest microphones in the world. Each model that leaves the factory floor exudes class, character, versatility, and reliability. And for those reasons, every studio wants to have at least one Neumann microphone in their locker.
Audio, however, is evolving. And while the amount of professional and expensive facilities is diminishing, musicians are becoming evermore savvy with recording and production while sitting in front of their laptops. Neumann, with Ralf Oehl at the helm, is moving with the times. Read on as we chat about Oehl’s passion for design, chasing perfection, and the company’s exciting new projects.
HAPPY: Germany has a proud history of design and manufacture, which spans many industries and stretches back several decades. Were you aware of that mighty presence all around you as you were growing up? Or was it something you took for granted?
RALF: Wow, that is an interesting perspective to start our conversation. In fact, ‘design’ was something that drew my attention from the very early days. As a kid, I would constantly make sketches of fantasy products, from cars to spaceships, from clothes to homes. I was surrounded and inspired by German designers and manufacturers, whether it was fashion designer Jil Sander, industrial designer Dieter Rams, cameras by Leica, my father’s Hi-Fi equipment from Braun and even his Sennheiser headphones. This was a steady passion in my life, to the point that when I graduated from high school, I had clear plans to become a designer. I ended up in a trainee program in the fashion industry and at my parents’ encouragement, split my studies between courses on design and on commercial tasks.
Eventually, the commercial side in me prevailed, moving on to strategy consulting, high-tech manufacturing and finally running my own investment company that focuses on scaling artisan manufacturing. But I have always maintained a strong appreciation for design, craftsmanship and quality materials. This capability of combining my creativity with my commercial influences has been a guiding thread throughout most of my career, reaching its pinnacle when I was given the opportunity to helm Neumann.
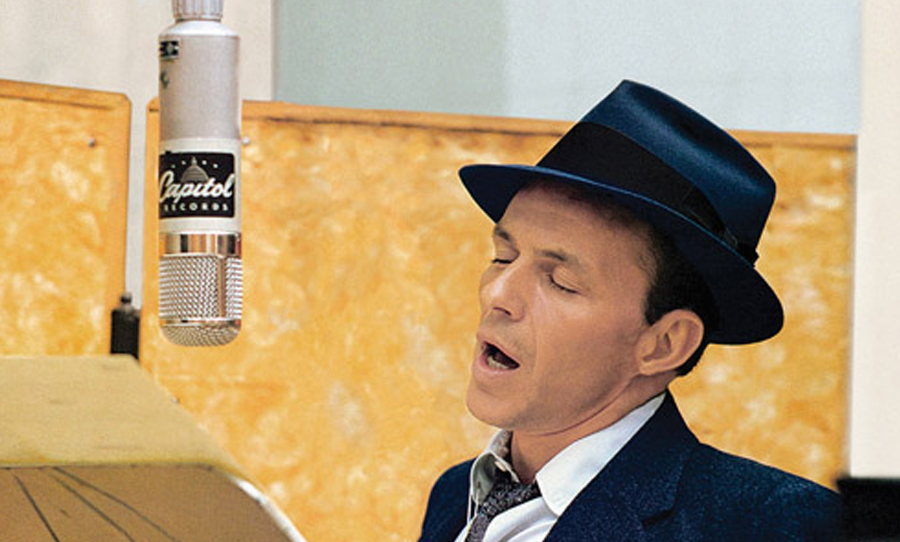
HAPPY: Neumann microphones have cut a unique silhouette for almost a century. Even for a layperson: they might see a picture of Frank Sinatra singing into a U 47 and instinctively recognise it as a high-quality product, for example. When did you first become aware of Neumann’s presence?
RALF: Truthfully, I was not aware of Neumann as a brand before I was considered for the CEO role two years ago. I had never worked in the pro audio world before, but was approached for the position due to my extensive experience with high-end manufacturers and high-tech products. However, as a passionate lifelong audio consumer, I immediately had familiarity with Neumann’s products. For instance, I was quickly drawn to the M 49, recognizing it as Barbra Streisand’s mic of choice, while also identifying the singular shape and iconic design of the U 67 and U 47, and many more classic microphones.
When I first visited the Neumann manufacturing site in Wennebostel, Germany, I had a great realisation that what sets Neumann apart is not merely the visuals and legendary style, but truly the quality of the materials and the level of craftsmanship that goes into it. The ruggedness, weight and quality of the components and artisanal, hand-crafted manufacturing process are unparalleled, and a big part of why more than 70% of the microphones we have manufactured in the last 90-plus years are still in circulation today. While visual aesthetics are important to me, I put more emphasis on durability and craftsmanship. When you first touch the surface of a Neumann microphone and experience the weight, attention to detail and precision, you’re taken to a whole new dimension.
HAPPY: The Neumann badge comes with a weight of responsibility. Any audio professional sees that logo and is instantly reassured that they’re dealing with a superior product. How does it feel knowing that there are such high expectations of every product that comes out of the Neumann factory?
RALF: In short: it feels amazing! As a person who is unabashedly obsessed with quality and perfection, I couldn’t ask for a more rewarding job than this one, where an ever-growing community of customers is just as enthusiastic about quality as we are. I also feel blessed to be surrounded by the most talented acoustic and electronic developers in the industry, some of the most extraordinary sound engineers and a tremendously skilled team of passionate craftsmen and women.
While there is a weight of responsibility to manage this in an economically feasible manner, we are all empowered and motivated by the fact that whatever solution we bring to market is expected to be a reference solution for the long haul. With this, we take our time to develop new products and make sure everything we release is as technically as close to perfection as possible, even if it requires longer development cycles than the broader industry.
For instance, our newly announced Miniature Clip Microphone took more than six years of development but is already on track to transform how the industry handles close-miking instruments. We’re grateful to our customers for their patience and support as we work tirelessly to engineer and craft the highest quality products, and are confident that it is well worth the wait.
HAPPY: Some Neumann products are understandably very expensive, yet the company has to compete for the dollars of working audio professionals (and hobbyists) too. How do you ensure that the standard of Neumann is met across the whole range?
RALF: Neumann is known for meticulous craftsmanship. All of our microphones and monitors are hand-crafted in Europe to ensure reliable and consistent quality – from our highest-end products, to the entry-level, budget-conscious offerings. As we are not willing to compromise on sound or build quality at any level, the way we make Neumann accessible with our more economic products is by reducing unessential features and simplifying components.
We work hard to ensure that everything we build will last for decades to come. For this reason, so many of our products retain or even increase in value over time. We are increasingly seeing our more classic microphones treated in the same way as Swiss watches – as a great, and sometimes first – investment in our customers’ pro audio careers, for both professionals and hobbyists.
HAPPY: It’s an exciting time to be in audio. The phenomenon of the bedroom producer marches on and the rapid innovation in software and hardware is there for all to see. How does Neumann plan to capture the attention of more and more people making music at home?
RALF: The audio industry is transforming, and it is exciting to see how much incredible music is being produced outside of the studio. Take Billie Eilish for example, who produced her Grammy-sweeping album When We Fall Asleep, Where Do We Go? with her brother Finneas from their bedroom studio using the TLM 103. We feel honoured and humbled to see Neumann products proactively chosen by artists around the world to create music at home.
We noticed early on that more and more artists are entering the industry without the use of traditional methods of recording – and not just musicians – this also is a trend amongst filmmakers, podcasters and even in gaming. In light of this shift, we have focused on education and have invested in our #AtHomeWithNeumann initiative which offers virtual tutorials, seminars and resources for aspiring and established audio creators to ease the transition to remote production. Remote, home studio productions are no longer just for entry-level, budget-conscious hobbyists. This has become professionalised and is commonplace with top artists and content creators as well.
We recently launched the MA 1 system to enable cohesive studio monitor setups in remote production environments and are planning more product launches to support remote and on-the-go audio production. We have also seen a constant increase in demand for high-quality basic products like the TLM microphone family and have responded in kind by almost tripling our hand-building production capacity in the past two years.
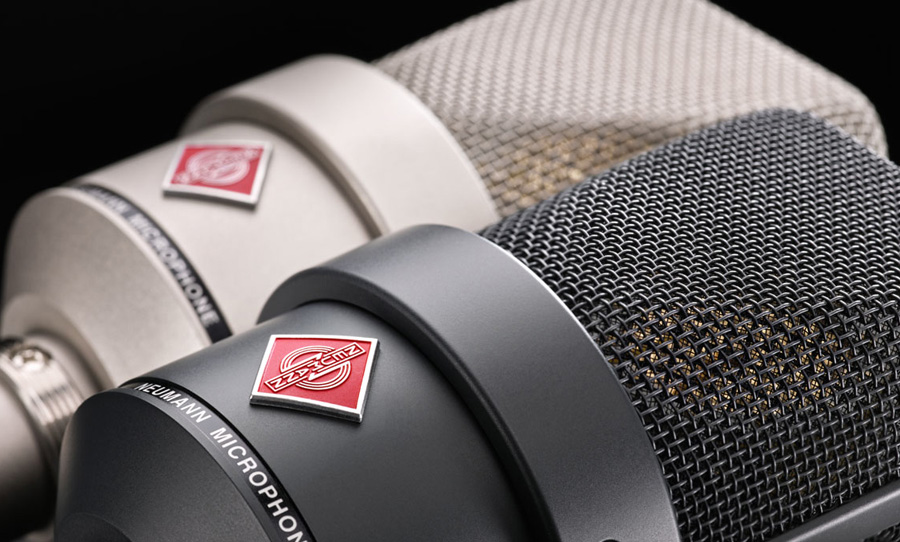
HAPPY: And on exciting times, Neumann has debuted its Miniature Clip Mic System, complete with a brand new electret capsule design. What inspired this latest innovation in Neumann microphone technology?
RALF: When we set our sights on adding a new product to the Neumann portfolio, it is always with the intention to solve a challenge that our customers are facing in their workflow that can’t currently be supported by our existing solutions. We maintain very close relationships with our customers, many of which are esteemed and experienced producers and front of house engineers.
These colleagues have expressed that they are looking to achieve the iconic “Neumann sound” when they need to use close-miking solutions, especially when they are in live environments that are ill-suited for studio-grade recording equipment, which leads to a significant drop in sound quality. Based on this recurrent feedback, we set out to create a solution that brought the signature Neumann sound quality to close-miking in live settings.
In the development process, we initially tried to solve this with a very small true condenser solution, but at some point, realized that it could not be done. In 2016, we made a bold choice to invent a completely new electret capsule that eliminated the disadvantages this technology was known for, while enabling the signature sound quality we are known for. From here, the KK 14, or Miniature Clip Mic, was born.
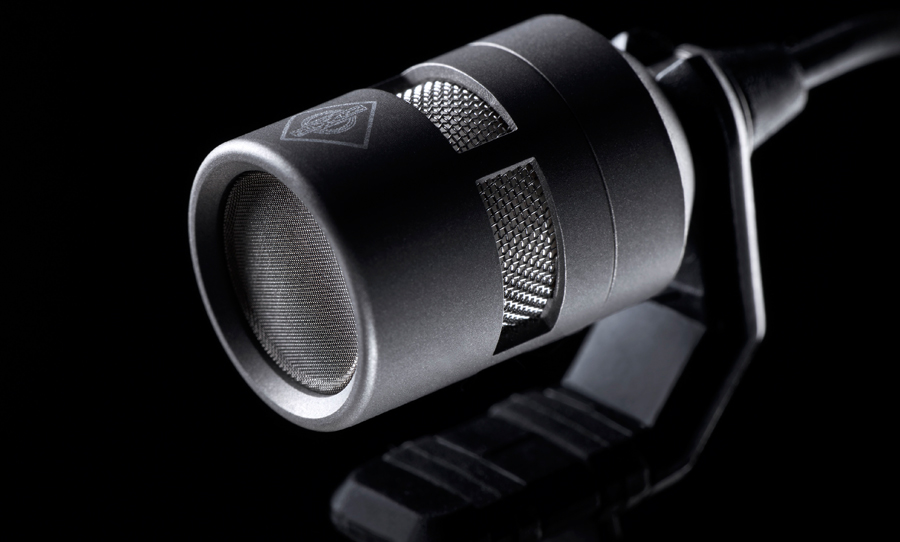
HAPPY: Neumann has quite a reputation to uphold. What kind of testing is involved to ensure that products like the Miniature Clip Mic System can withstand all the rigours of the orchestra or even the drum kit?
RALF: At Neumann, we only release products that we are certain will be reference solutions in the market for years to come, so we take the development and design phase very seriously. We took our time with the Miniature Clip Mic System to make sure we got it right. Not only the capsule, but the entire modular concept with its very critical mounting solutions and other accessories endured numerous reviews and optimisation cycles over the past six years. There are sound reasons for why we chose titanium housings over much cheaper aluminium and added kevlar threads into our cables.
In tests and trials with accomplished musicians using the Neumann KK 14 electret capsule, a cardioid directional pattern was identified as the best solution to deliver both an open sound and a sufficient degree of isolation. The capsule’s directivity is constant throughout the entire frequency range and therefore offers sufficient isolation from nearby instruments, even in the fundamental frequency range.
At the same time, our new electret microphone design was developed to handle 153 dB SPL, while operating with very low self-noise — which again is important in capturing softer sounds. This is the result of the interaction between the relatively large diaphragm and circuit design. In this respect, the microphone benefits from our decades of development experience in circuit design, even if the power supply is limited.
Sonically, we achieved a balanced, neutral frequency response as well as a refined impulse reproduction. When our new system was applied to diverse instruments such as strings, brass, drums, percussion, and piano, the sound was both detailed and natural. Throughout our design process, special attention was paid to properly capture the fundamental frequency of the instruments, which can be a challenge with competitive microphone solutions.
Aside from sonic requirements, it was very important for us to ensure that the new microphone also delivered on build quality and ROI — which is particularly important for rental companies. Therefore, we chose a titanium housing for the capsule, which is robust and provides protection for all the internal elements. Meantime, a modular design means that the capsule can be separated from the associated gooseneck so individual components can be replaced if necessary.
HAPPY: Neumann has always been adept at moving with the times in the audio space. Do you have any predictions and/or plans for the future of audio?
RALF: The future of audio is looking bright and more diverse than ever before. We are very excited to help pave the way for some monumental shifts underway in the industry. At this stage, we are focused on a few primary areas: immersive audio, the return to live music, and remote workflows.
Immersive audio is becoming increasingly popular in music, film and gaming. As a company that has pioneered binaural audio production and recording for decades with such products as the KU 100, and in more recent years our KH series of studio monitors, we are eagerly looking at how we can continue this legacy by growing and adapting our product line-up with new solutions for this category.
As live music returns on the back of the pandemic, we are also seeing some fascinating trends, largely driven by the metaverse and prevalence of immersive audio in gaming. Live concerts will still happen in-person, but we will continue to see virtual performances become commonplace. Here, we are proud to offer best in class solutions like the new Miniature Clip Microphone to enable superior sound, regardless of whether the concert is enjoyed from the front row, or in one’s living room.
Finally, as professional audio production is no longer exclusive to recording studios, we are continuing to expand our product portfolio and existing solutions to support this new way of work. We are particularly looking at how our product suite can enable consistency in audio quality for remote productions and are continuously seeing how we can adapt our offerings to best equip home and on-the-go studios. An open-back reference headphone may be a sound next step.
For more info on Neumann, visit the website.